Outsourcing printed circuit board assembly, mechanical sub-assembly and complete finished products can contribute significantly to an electronic equipment company's profitability and return on investment.
Potential benefits include lower product cost, faster product introductions, higher quality and lower asset investment. Outsource manufacturing strategy not well conceived, however, can result in inflated product cost, delayed product introductions, missed deliveries and higher customer returns. There are many excellent outsourcing relationships, but there is more trial and error in selecting suppliers of electronic manufacturing services (EMS) than many realize. Since a company’s investment in tooling and training is not readily transferable from one supplier to another, the cost of terminating a poor or sub-optimal outsource program can be substantial.
CMC identifies the most suitable EMS contractors and sites for our client needs. We have extensive knowledge and contacts with large and smaller specialized contractors in the Americas, Asia and Eastern Europe. We perform in-depth, comprehensive requirements analysis of our client's assembly, test, quality control and special service needs to recommend differentiable supplier evaluation and selection criteria.
Qualification of contract manufacturers involves expert on-site factory audits, bid package creation, analysis of incoming proposals and due-diligence investigation. Factory qualification audit-surveys focus on those capabilities key to client programs success. Our process provides a solid base for recommendations rather than relying on polished presentations and plant tours, which sometimes are not true representations of services delivered.
ELECTRONICS MANUFACTURING SERVICES (EMS)Supplier Selection Issues
- Simple, medium or advanced technology site?
- Special process needs or DFM issues?
- Materials management complexity and acquisition issues?
- Best fit “delivery system” in terms of mix, volume, cycle times?
- Special in-process test or functional test needs?
- Frequency and urgency of change orders - ECO’s and PO’s?
- Batch production or continuous in-line build?
- Special regulations or certifications?
- Volume box-build or CTO/BTO, bulk distribution or fulfillment?
- Integration importance of cable assembly, metal fabrication or plastics?
- Large, medium or smaller size CEM?
- Possible advantages/disadvantages of international?
- Possible advantages/disadvantages of using multiple CEM's?
- Importance of other technical services now or in the future?
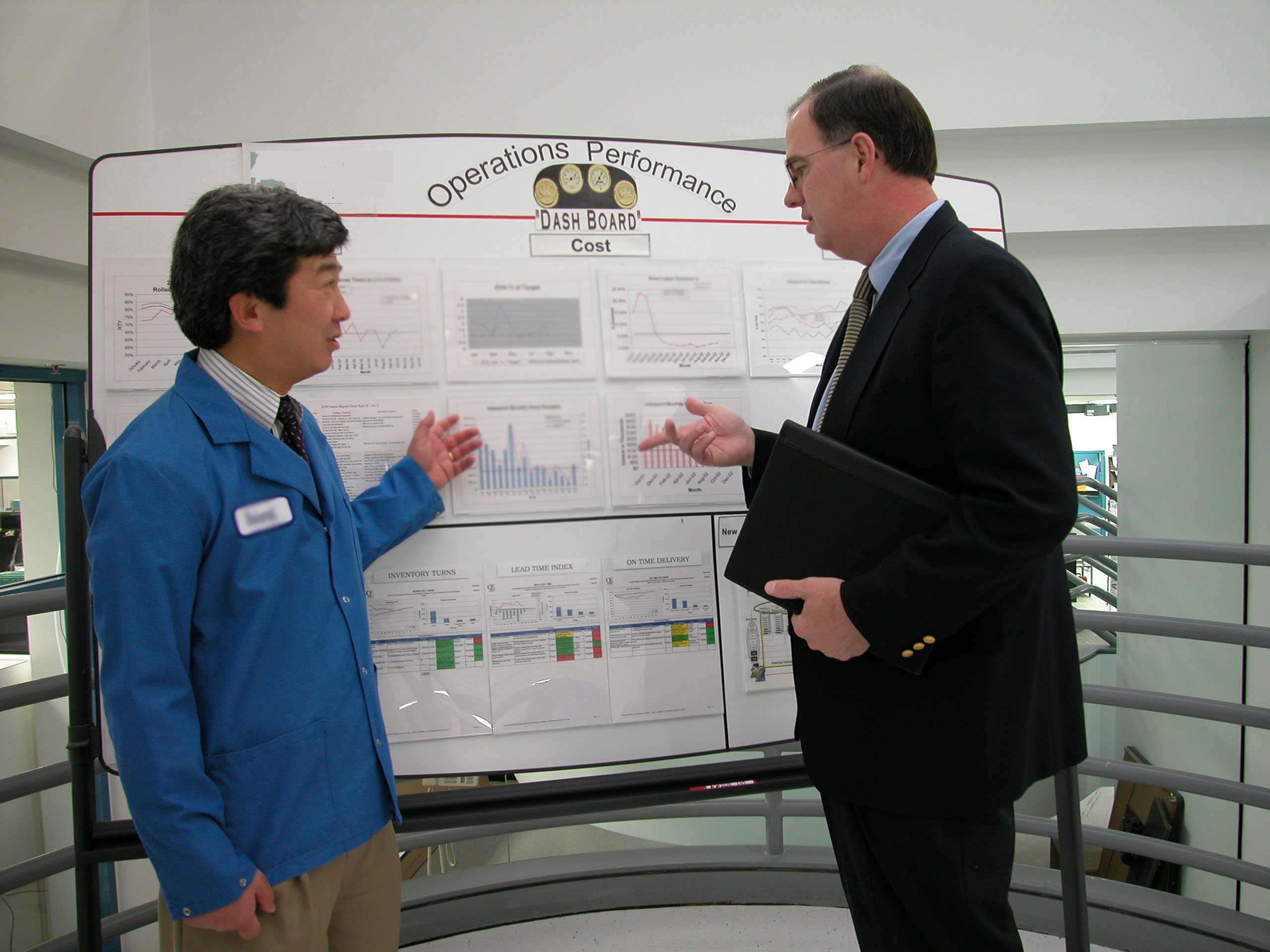